Hot Air Nonwoven Fabric in the Diversion Layer
Here’s how Hot Air Nonwoven Fabric in the Diversion Layer is typically produced:
- Raw Material Preparation: Selection of fibers, including conductive materials like carbon fibers or metal-coated fibers.
- Web Formation: Carding and laying the fibers into a continuous web.
- Bonding: Hot air through bonding to bond the fibers while maintaining the conductive properties.
- Finishing: Calendering to smooth the fabric and cutting to the desired size.
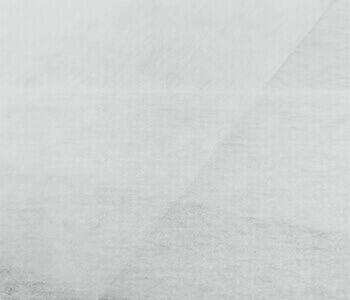
key Characteristics
Electrical Conductivity
- Conductive Fibers/Coatings: Incorporates materials like carbon, silver, or conductive polymers to provide electrical conductivity.
- Consistent Performance: Ensures reliable conductivity across the entire fabric.
Softness and Flexibility
- Comfortable: Maintains a soft feel, making it suitable for direct skin contact applications.
- Flexible: Easily conforms to various shapes and surfaces, enhancing usability in diverse applications.
Breathability
- Air Permeability: Allows air to pass through, ensuring comfort and ventilation, especially in wearable applications.
Durability
- Mechanical Strength: Retains the strength and tear resistance of traditional nonwoven fabrics, ensuring long-lasting performance.
Lightweight
- Low Weight: Lightweight nature enhances comfort and usability without adding bulk, crucial for wearable applications.
Thermal Stability
- Heat Resistance: Withstands a range of temperatures, making it suitable for applications requiring thermal stability.
Chemical Resistance
- Resistance to Chemicals: Resists degradation from exposure to various chemicals, enhancing its durability in different environments.
Eco-Friendly Options
- Sustainability: Can be manufactured using eco-friendly processes and materials, offering a sustainable option for environmentally conscious applications.
Application
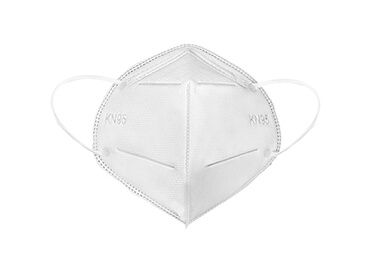
MEDICAL
Disposable KN95/N95 Mask
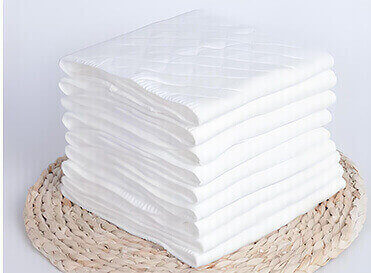
HYGIENE
Baby diapers, adult diapers, pads, adsorbentscleaning wipes